Robotic Arms: A Brief
This article gives a brief history of Robotic Arms and discusses their different types and various uses.
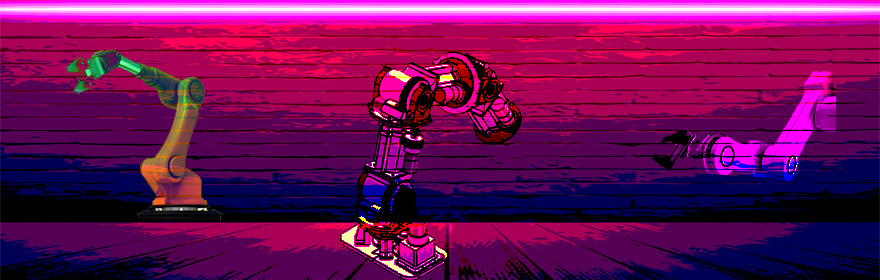
Most of the world’s robots are designed for hard, repetitive production work. They perform activities that human beings find complicated, dangerous or tedious. The most common production robot is a robotic arm.
A robotic arm is a device that is programmed to carry out a particular task with extreme accuracy at a rapid pace with great efficiency.
History of the arm
The idea of a robot arm is not new. The first robotic arm was designed by Leonardo da Vinci in the late fifteenth century. While analyzing his papers in the 1950s researchers discovered that he had sketched a robotic arm and humanoid figurines which could run on the clockwork technologies available at that time. It used pulleys, weights and gears to provide a partially autonomous motion. This design was assembled in 2002 also termed as the robotic knight which could walk and wave without manual intervention. The arm had 4 degrees of freedom and an analog onboard controller for supplying power.
In 1941, Isaac Asimov published a short science fiction story in the magazine where he introduced the Three Laws of Robotics thereby coining the term robotics. He later published the book “I, Robot” in which the characters obeyed the Three Laws of Robotics. This inspired engineer Joseph Engelberger and inventor George Devol, who filed for a patent for a programmed article transfer device — the first version of the robotic arm. In 1961, they started Unimation Inc. which focused on the manufacture of industrial robots. Their flagship was the Unimate 1900- a simple robotic arm.
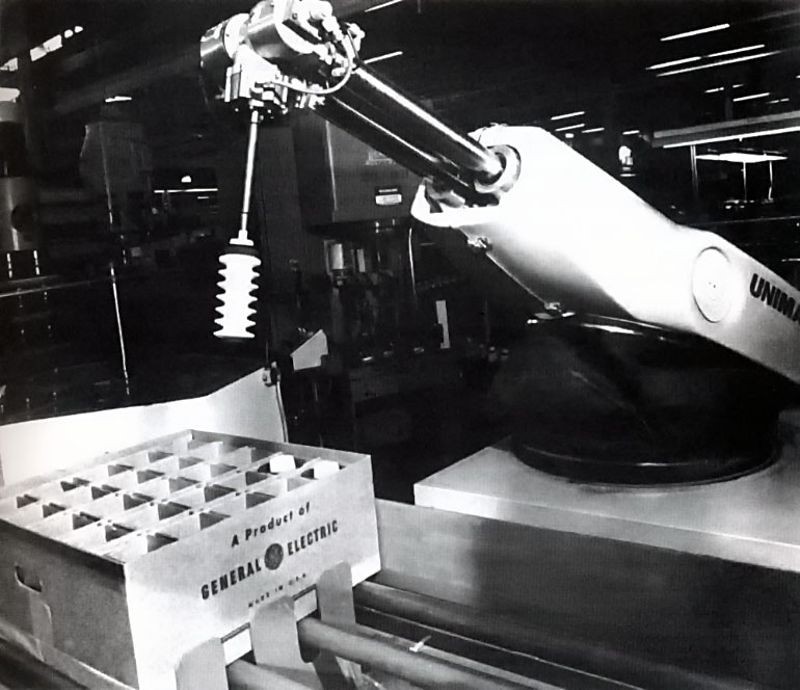
Unimate Robot
In 1963, researchers at the Rancho Los Amigos Hospital in California developed the Rancho Arm to help move disabled patients. It was the first computer-controlled robotic arm and was equipped with six joints to let it move like a human arm. Engelberg would further travel to Japan to partner with Kawasaki Aircraft to manufacture and sell Unimation’s robots in Japan.
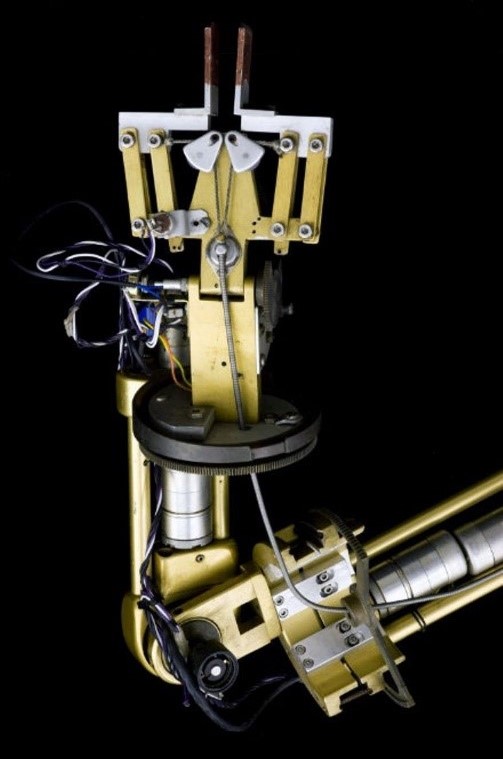
The Rancho Arm
In 1968, on the same principles as that of the Rancho Arm, Marvin Minsky developed the Minsky Arm which had 12 joints which could be controlled by a joystick. The arm was powered by hydraulic fluids. It was used for gentle lifting of the patients.
In 1969 Scheinman’s Stanford Arm robot achieved a milestone as the first successful electrically driven, computer- controlled robot arm. By 1974 it was able to guide itself through optical and contact sensors. It was the first arm to provide tactile feedback to its operator.
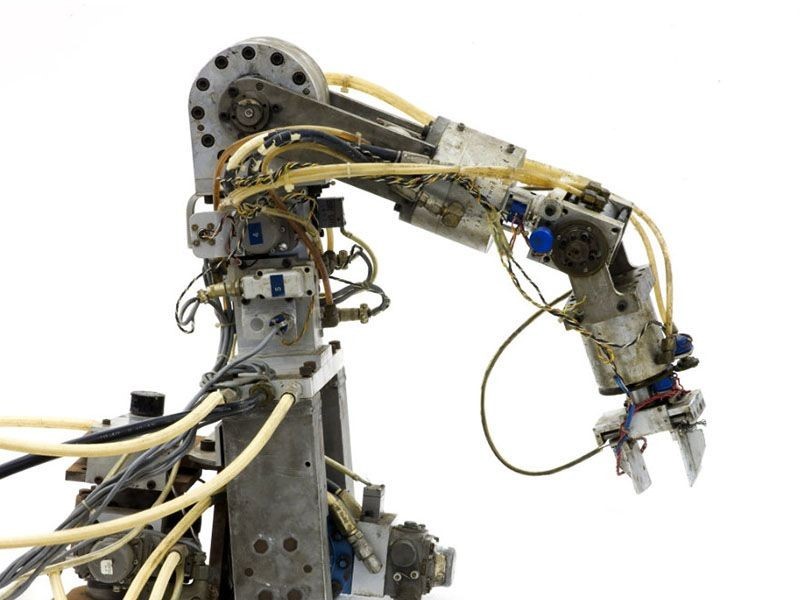
The Stanford Arm
In 1973, a German company Kuka launched Famulus - a robotic arm which worked by using six electromagnetic axles. This was revolutionary.
The CMU Direct - drive Arm I was built in 1981 at the CMU Robotics Institute. This arm had motors installed directly into each joint. The need for chains or tendons used in previous arms was removed by the electric motors housed within the joints. DD arm was faster and more accurate than its counterparts at that time.
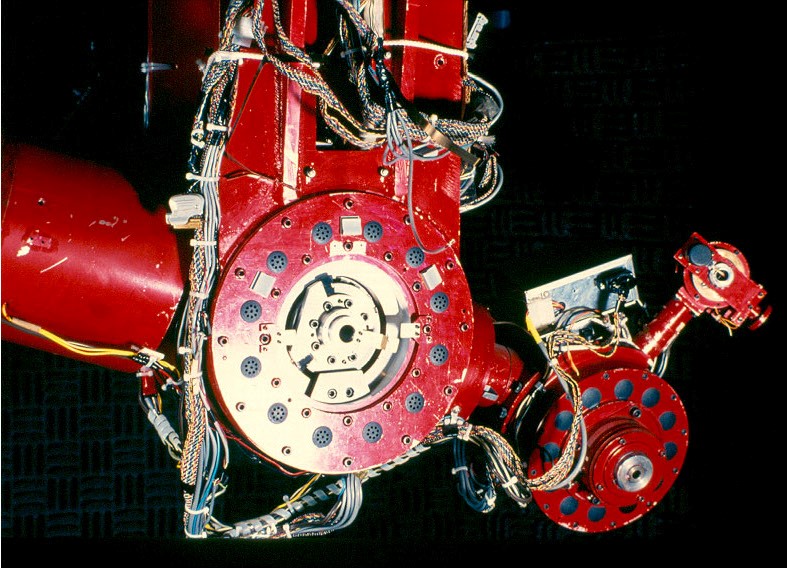
CMU Direct Drive Arm I
Currently every automobile manufacturer in the world employs robotic arms in factories for different operations.
Some examples of modern-day industrial robot arms include the UR series by Universal Robots and the Kuka arms by Kuka robotics.
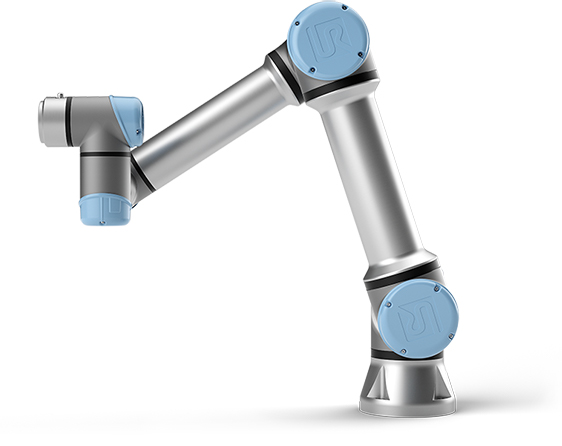
The UR5 Robot Arm
Construction of a robotic arm
The entire system of a robotic arm is based on two elements: the mechanical component and the signal processing component. The signal processing component processes the computational language which is uploaded on the processing unit whereas the mechanical portion is the design of the functioning arm using mechanics.
An industrial robotic arm consists of a series of joints, articulations and manipulators that work together to closely resemble the motion and functionality of a human arm. Depending upon the specific task expected by the robotic arm to perform it can have varying number of degrees of freedom i.e., different modes in which it can move. Generally, the motion of a robotic arm is determined under three categories: Roll, Pitch and Yaw.
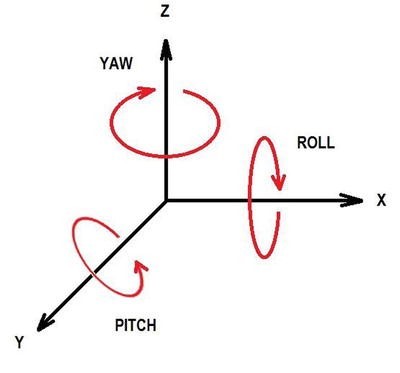
Roll, Pitch and Yaw
A human hand has pitch and roll along the shoulder; pitch and yaw along the arm and roll, pitch and yaw along the wrist giving a total of 7 degrees of freedom. The wrist or hand part of the robotic arm is also called the end effector.
A large portion of smaller robotic arms which are used in industries are benchtop mounted and electronically controlled. The larger versions might be floor mounted. They are generally manufactured using sturdy and durable metal like steel and cast – iron. These arms have 4-6 articulating joints used to replicate the human equivalents like wrist, shoulder, elbow, and forearm.
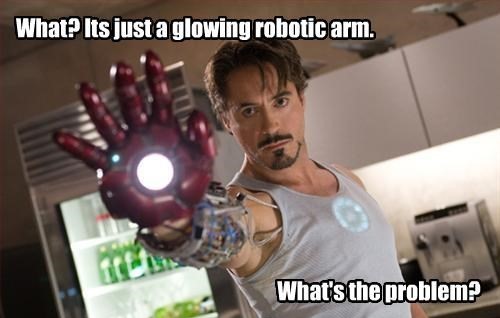
Types of Robotic Arm
There are various distinct robotic arms available today each manufactured for a particular role with special abilities suited for that environment. A large chunk of arms has six joints connecting seven sections but the key distinction lies in the manner in which the joints are designed to articulate and the range of movements they can perform. Some major types of robotic arms are:
Cartesian or gantry robotic arms: These arms consist of three articulating joints that are coincident with the cartesian axes X, Y, and Z. The directions are given in the form of cartesian coordinates to specify movement in three dimensions. Additionally, there may be a wrist joint which provides rotational motion. They are used in picking and placing objects and assembly operations.
Cylindrical robotic arm: This is the arm whose axes form a cylindrical coordinate system. They are used for handling machine tools, assembly operations and spot welding.
Spherical or Polar robotic arm: This is the arm whose axes form a spherical coordinate system. It is mainly used in die casting, welding, and fettling machines.
SCARA robotic arm: The term SCARA stands for Selective Compliance Assembly Robot Arm or Selective Compliance Articulated Robot Arm. To provide enforcement in a plane, this arm features two parallel rotary joints.
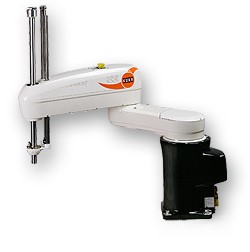
SCARA by KUKA
Articulated robotic arm: These are robotic arms having at least three rotary joints. They are typically used for assembly operations, die casting, gas welding, arc welding, fettling machines and spray painting.
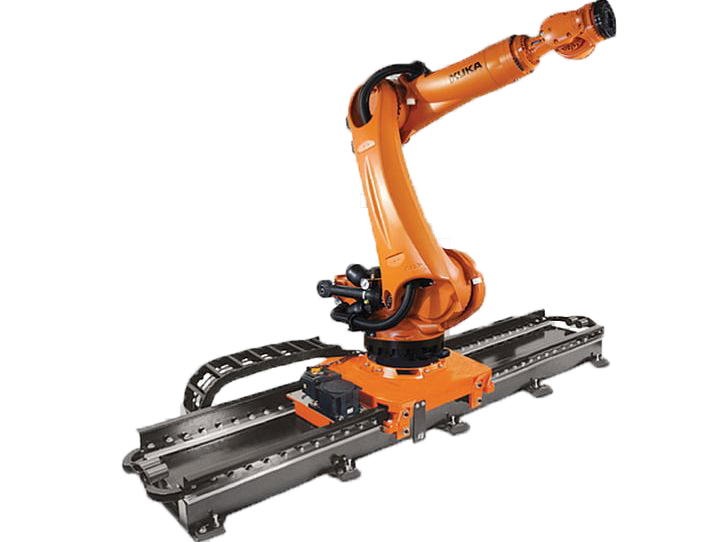
Articulated Robot by KUKA
Uses of Robotic Arm
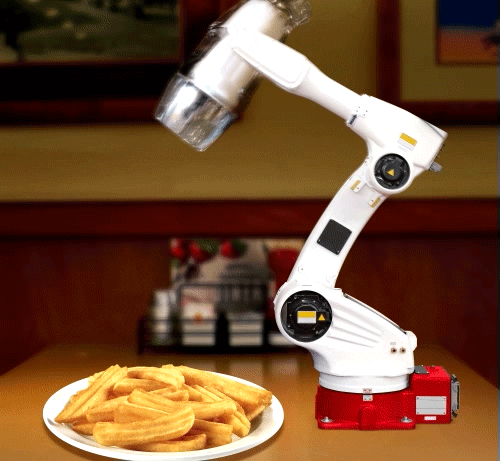
GIF from giphy
Other than being used as a salt shaker a robotic arm has various applications.
A robotic arm greatly increases the production rate and accuracy of placement and picking tasks. They are also used for other industrial applications like welding, painting, and drilling. They are also used in servicing of nuclear power plants, thermal power stations and cleaning up radioactive wastes.
The arm has applications in space exploration involving the repairs of the space station and collection of samples when mounted on top of a rover.
By using sensors and cameras with the arm, they can be used in rescue and relief operations. The assistance of a robotic arm is used in performing surgeries.
After installing barcode scanners on the arm, they are used in inventory management.
With the advancing technology, the cost of manufacturing different components of a robot has decreased. This has led to a rapid expansion in the affordability and availability of robots not only for large scale operations but also for small scale operations. With the extensive ongoing research and innovation in areas like computer vision and reinforcement learning, the applications of a robotic arm will continue to increase further. Until then
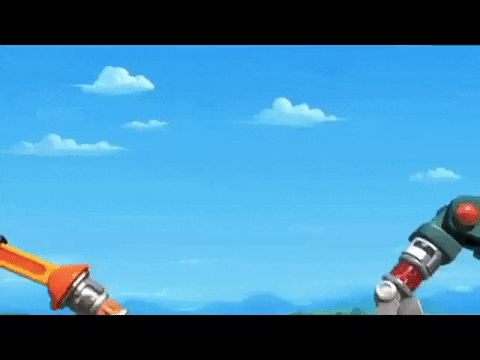
GIF from giphy
References
- Why Was the Robotic Arm Invented? by Megan Ray Nichols
- Assembling and Controlling a Robotic Arm by Manoel Carlos Ramon
- Timeline of Computer History